A Comprehensive Overview to Welding Inspection Madison Criteria
A Comprehensive Overview to Welding Inspection Madison Criteria
Blog Article
The Significance of Thorough Welding Inspection in Industrial Applications
In the world of commercial applications, the importance of meticulous welding examination can not be overemphasized. It plays an important role in making certain the architectural integrity and long life of bonded components. Advanced non-destructive screening strategies enable for the very early discovery of potential issues, such as splits and incomplete fusion, which, if left uncontrolled, might lead to tragic failings. Moreover, adherence to rigorous market standards not just ensures top quality however likewise builds customer confidence. As we discover the multifaceted advantages of diligent welding evaluations, one have to think about the more comprehensive implications on safety and security, reliability, and cost-effectiveness in industrial procedures.
Enhancing Structural Integrity
When it pertains to welding examination in industrial applications, enhancing structural stability is vital. The key objective of welding examination is to make certain that the welds are qualified of birthing the anticipated loads and tensions they will experience in service. This includes a detailed analysis of the welds' measurements, placement, and total top quality, guaranteeing they fulfill the defined criteria and codes. Specific examination approaches, such as aesthetic assessment, ultrasonic testing, and radiographic testing, are important in determining issues that could compromise the framework's safety and security and capability - Welding Inspection Madison.
The value of preserving structural honesty in bonded structures can not be overstated. Badly performed welds can lead to tragic failings, resulting in pricey fixings, downtime, and even endangerment of human lives. For that reason, inspectors play a critical duty in the lifecycle of commercial elements, providing guarantee that the welding process delivers the wanted stamina and durability.
Moreover, advanced modern technologies, such as phased range ultrasonic screening and electronic radiography, offer improved capacities in discovering possible weaknesses, enabling corrective steps prior to issues intensify. By focusing on the integrity of welds through careful inspection, markets can make sure operational efficiency and prolong the long life of their framework.
Identifying Welding Problems
Recognizing welding defects is an important facet of ensuring the security and dependability of bonded frameworks. These issues can compromise the integrity of the entire setting up and, if left unaddressed, might lead to devastating failures. Usual welding issues consist of porosity, cracks, incomplete combination, and damaging. Each of these issues occurs from certain reasons, such as incorrect welding strategies, contamination, or poor warmth control.
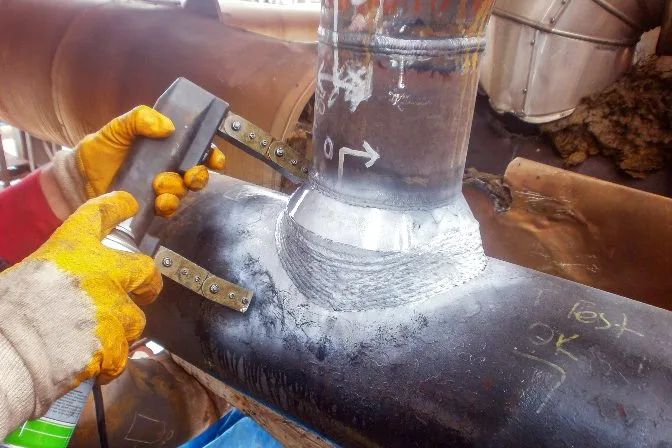
Competent inspectors use both aesthetic examination and advanced non-destructive screening (NDT) approaches, such as ultrasonic or radiographic screening, to identify these problems. The timely recognition and rectification of welding problems are imperative to preserve the architectural honesty and longevity of industrial elements.
Making Certain Compliance Specifications
Compliance with well established requirements, such as those provided by the American Welding Culture (AWS) and the International Organization for Standardization (ISO), guarantees that welds fulfill minimal safety and security and quality requirements. These requirements incorporate a wide array of requirements, including material specifications, welding treatments, and credentials of welders.
Regular audits and examinations are necessary in verifying conformity. Examiners must have a comprehensive understanding of the pertinent standards and be experienced at utilizing different non-destructive testing (NDT) methods to review weld quality. By making certain that welding practices straighten with compliance requirements, companies alleviate the risk of non-conformity, which can cause lawful obligations and safety and security hazards.
Additionally, maintaining compliance not just safeguards structural stability yet also improves a firm's credibility in the sector. Stakeholders and customers are extra likely to depend on firms that continually demonstrate a dedication to quality and security through extensive compliance. Thus, making certain conformity standards is a crucial element in the effective implementation of welding in commercial applications.
Lowering Maintenance Expenses

The application of advanced non-destructive testing (NDT) techniques, consisting of ultrasonic, radiographic, and magnetic particle inspections, boosts the capability to spot subsurface imperfections without jeopardizing the structural honesty of components. By using these methods, sectors can substantially extend the life span of their equipment, lowering downtime and the associated economic burden of upkeep tasks.
Moreover, a robust welding assessment regime sustains the optimization of upkeep routines, changing from reactive to predictive upkeep techniques. This aggressive method not just curtails unforeseen failings but likewise simplifies resource allotment, making certain that maintenance efforts are concentrated and reliable. Ultimately, the financial investment in rigorous welding assessment is offset by the substantial financial savings realized with lowered upkeep demands, adding favorably to the overall operational effectiveness of commercial ventures.
Improving Safety Steps
Although safety and security is a paramount issue in industrial procedures, attaining optimum safety and security standards requires a specialized concentrate on the top quality and integrity of bonded frameworks. Welding inspection plays an important duty in this context, as it makes certain that all joints about his and connections meet stringent safety criteria. Comprehensive inspections help identify problems such as cracks, porosity, or incomplete combination that might compromise structural integrity. Such defects, if left unaddressed, position considerable dangers, potentially causing disastrous failings.
Approaches like ultrasonic testing, radiographic testing, and magnetic fragment inspection enable for thorough examination without damaging the framework. Applying a robust high quality control system that consists of normal training for examiners and welders makes certain adherence to established security requirements.
Last but not least, fostering a culture of security within the company stresses the relevance of comprehensive welding assessments. Urging open interaction and collaboration among engineers, welders, and examiners adds to a common you can try this out dedication to safety and security quality. Welding Inspection Madison. In doing so, sectors can guard their procedures, shield personnel, and maintain public trust

Verdict
Extensive welding inspection is vital in industrial applications, significantly improving architectural stability and integrity. Eventually, the thorough implementation of welding inspections plays a vital role in preserving functional efficiency and safety and security in industrial settings.
As we discover the multifaceted benefits of attentive welding inspections, one need to consider the wider effects on safety, reliability, and cost-effectiveness in commercial procedures.
The primary goal of welding assessment is to make certain that the welds are capable of bearing the expected lots and stresses they will certainly run into in service. Effective welding evaluation plays an indispensable duty in minimizing these costs by guaranteeing the stability and long life of welds, therefore mitigating the risk of premature failures.Extensive welding assessment is crucial in commercial applications, significantly enhancing structural integrity and reliability. Ultimately, the diligent execution of welding inspections plays see here an essential role in maintaining operational efficiency and safety in commercial setups.
Report this page